The simple answer is yes.
But if you’re like us, you don’t want just the simple answer. We’re very excited to tell you the story about how we went about cutting silicon nitride with one of our waterjet cutters.
An engineer from Stein Seal Company contacted us wanting to know if we could cut several 1/8” wide slices from a small 1” thick block of silicon nitride. They work with this material all the time, but the brittleness of the material would have made it very difficult to create such fragile parts without breaking them. A waterjet cutter is a tool that specializes in doing things that are hard for many other cutting methods. Waterjet cutting happens to be our specialty, so we said yes. Here’s the story of what happened after we said yes.
Silicon nitride (Si3N4) is a chemical compound of the elements silicon and nitrogen. It is extremely hard, very resistant to wear, is able to be used in extremely high or low temperatures, and has excellent resistance to fatigue. These qualities make it very useful in many specialized applications. The attribute of greatest interest to us was its hardness, which is 8.5 on the Mohs scale. The reason this posed a problem for us is that the abrasive we use in waterjet cutting has a hardness of about 7, and everyone knows that your cutter needs to be harder than the thing you are cutting. In fact, the Mohs scale, which was developed long ago by a geologist, is really just a comparative scale of a material’s resistance to being scratched. If you find a stone that can be scratched with Diamond (10) but cannot be scratched with Topaz (8), then you must be at about a 9 on the Mohs scale.
We’ve had some experience cutting really hard stuff, so we knew we would need an abrasive that was harder than garnet. Garnet is the most common abrasive used in waterjet cutting because it is both very hard and readily available. It is the most cost-effective solution for a wide range of materials. The material we needed to cut now required us to go all the way to the top. We chose a product called silicon carbide (also known as carborundum), which has a hardness of 9 on the Mohs scale. This abrasive is hard enough for the job, but has the unfortunate side effect of being harder than our tungsten carbide nozzles. So we ordered a few Roctec 500 nozzles, because we knew that this abrasive was going to make lunch out of the nozzle, and we wanted to make that lunch last as long as possible. At $140 apiece, these nozzles cost 75% more than the Roctec 100 nozzles we normally use and only last 30% to 40% longer.
Next, we rigged up a special redneck system for delivering the abrasive to the cutting head so we wouldn’t contaminate our normal system. Finally, we made a simple little fixture consisting of a steel support plate with a piece of plywood on top to hold the part really nice and snug without needing any clamps. The plywood adds to the redneck appearance which we were pretty committed to already by this time.
Now comes the fun part! We’ve got 87,000 psi of water pressure mixed with some super-hard, sparkly, black abrasive; a little white hopper ratchet strapped to the waterjet; wire ties and tape holding various tubes and apparatus in place; and a bunch of waterjet geeks standing around with goofy grins on their faces. What’s going to happen? What cut speed should we start with? Is the abrasive hopper going to come crashing down on our heads? Is the nozzle going to blow up and throw shrapnel all over the place?
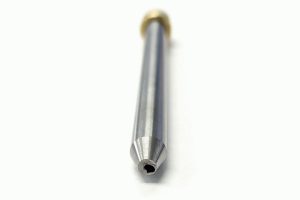
Waterjet nozzle after less than 10 minutes of cutting! It doesn’t take a professional to see that this is not optimal.
Here’s what ended up happening. We decided to start out with an abrasive flow rate of 1 lb/min and a cut speed of .1 in/min. After restarting and increasing the cut speed several times, we ended up at .3 in/min and decided to finish the first cut at this rate. This was obviously still too slow, but we couldn’t know how much too slow until the cut was finished and we could look at the cut surface. Trying to cut a brittle material too fast can cause it to break, and we wanted at least one good slice for our efforts.
The first slice had a cut time of less than 10 minutes. Before the cut was even done, we could see by the appearance of the water stream that the waterjet nozzle was already starting to go bad. Imagine our surprise when we pulled the nozzle out and discovered that it was completely toasted! The waterjet had eaten our nozzle in less than 10 minutes!
This short video shows the action inside the cut. (Sorry the quality is so poor. We’re better at waterjet cutting than we are at taking videos…) As strange as it may seem, waterjet cutting almost always generates sparks, even when cutting materials that you wouldn’t expect would spark, like glass. For whatever reason, this exact combination of material and abrasive made the action inside the cut much more visible than we’ve ever seen before, so this was particularly exciting for us.
The cut face of the finished slice had a very interesting story to tell as well. We had never before seen the entire life story of a nozzle told in one 2” long cut. Take a look at the photo of our first 2″ long cut… The waterjet cut from left to right. The first mark about ¼” in from the end was where we stopped and restarted, so that can be ignored. But less than half way through the cut, some really funky stuff starts happening. The most puzzling part of all is that the worst of it is at about the center of the cut, after which the cut quality starts to look nicer again. However, in waterjet cutting, it’s not all about “looking nice”. A quick glance around the group gathered by the waterjet was proof of that! The slice also gets wider at the bottom as the cut progresses, showing that the stream was no longer cutting straight.
We decided to majorly decrease the abrasive flow rate in hopes of getting the nozzle to last at least long enough to make one nice cut. Our smallest metering disk yielded a flow rate of about .3 lb/min, less than one third of the starting rate. We also doubled the cut speed for a rate of .6 in/min. These settings proved to be a success, producing a cut quality that was fairly rough, but at least we had left the realm of complete guesswork and were back in normal territory. A third cut at .25 in/min and a fourth at .18 in/min kept sneaking in on the nice smooth cut and optimal cut speed that we were looking for. After the fourth cut, we had a little over 20 minutes on our second nozzle. It was still producing half decent results but was beginning to show enough wear that we decided it needed to be retired.
Just for fun, we decided to see what the cut face looks like up close. The photo at 120x magnification shows pretty much what we would expect to see from a smooth waterjet cut. Waterjet cut finishes are rated by their visual appearance without the aid of magnification, not by any standard surface finish scales like RA or RMS.
Before calling it quits, we decided to make a few cuts in mild steel just for fun. To better compare with our normal cutting settings, we changed the abrasive rate back to 1 lb/min and did a test in 2-1/2” thick steel and another in 1/4″ thick steel. To our surprise, these tests both showed the same thing—the harder abrasive provides little to no advantage when cutting something as soft as mild steel. As counterintuitive as this may seem, the reason is quite simple—garnet is already much harder than steel, so there isn’t much to be gained by using an even harder abrasive.
Optimal cutting will only be achieved with an abrasive media that is considerably harder than the material being cut. Regardless of the abrasive being used, there is a very strong correlation between cut speed and the hardness of the workpiece. However, as the hardness of the work piece approaches the hardness of the abrasive, you will start to spin your wheels, figuratively speaking, and may need to consider using a harder abrasive.
At AquaJet Services, we welcome opportunities to learn and are not afraid to tackle difficult projects. If you have a challenge on your hands and you’re not sure if a waterjet is the tool for the job, just give us a call! Our goal is to help our customers find the right solution for their needs, whether that involves waterjet cutting or not.
If you found this article interesting and would like to learn more about waterjet cutting, take some time to look at the learning resource on our website and sign up for our e-newsletter. It’s worth your time!
-The crew at AquaJet